SUS 410S Stainless Steel Pipe Welded Round Tubes
Overview
410 stainless steel pipe is made up of martensitic steel. Martensitic steels are used when the strength and toughness are needed along with high wear and tear resistance. Their corrosion resistance is lower than the austenitic stainless steels in general. The 410 stainless steel pipe material has carbon, manganese, silicon, phosphorus, sulfur, chromium and nickel in its material composition. This specific composition provides it with the high wear and tear resistance. Any 410 grade pipe can be manufactured through cold drawing as 410 seamless pipe or through electric resistance weld or through electric fusion weld. The 410 stainless steel pipe dimensions vary according to the manufacturing methods as well.
Physical Properties
Magnetic Permeability | 0.28 lb/in3 7.73 g/cm3 |
Specific Heat | 0.11 BTU/lb-°F (32 – 212°F) 0.46 J/kg-°K (0 – 100°C) |
Modulus of Elasticity | 29 x 106 psi 200 GPa |
Thermal Conductivity 212°F (100°C) | 187 BTU/hr/ft2/ft/°F 26.9 W/m-°K |
Melting Range | 2700 – 2790°F 1480 – 1530°C |
Electrical Resistivity | 23.7 Microhm-in at 68°C 60 Microhm-cm at 20°C |
Mechanical Properties
Material Grade | Material Number | Tensile Strength Rm N/mm² Ksi (MPa) min |
Yield Strength Rp0.2% N/mm²Ksi (MPa) min |
Elongation (%) |
Brinell Hardness HBW max |
Rockwell Hardness HRB max |
TP410 | S41000 | 60 (415) | 30 (205) | 20 | 207 | 95 |
Corrosion Resistance
410 stainless steel resists dry atmosphere, fresh water, mild alkalies and acids, food, steam and hot gases. Must be hardened for maximum heat and corrosion resistance. Performance is best with a smooth surface finish. Less corrosion resistant than the austenitic grades and also less than 17% chromium ferritic alloys such as Grade 430.
Heat Treatment
Full anneal – 815-900°C, slow furnace cool to 600°C and then air cool.
Process Anneal – 650-760°C and air cool.
Heat to 925-1010°C, followed by quenching in oil or air. Oil quenching is necessary for heavy sections. Temper, generally within the range 200-400°C, to obtain a wide variety of hardness values and mechanical properties as indicated in the accompanying table.
The tempering range 400-580°C should generally be avoided.
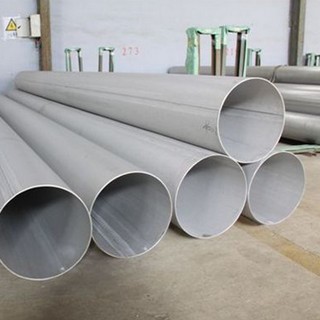
