SS 410S Sheet Metal Aisi 410S Stainless Steel Sheet Price
Product Description
Alloy 410S (UNS S41008) is a low carbon, non–hardening modification of Alloy 410 (UNS S41000) the general purpose 12% chromium martensitic stainless steel. The low carbon and a small alloy addition minimize austenite formation at high temperatures which restricts the alloys ability to harden. 410S remains soft and ductile even when rapidly cooled from above the critical temperature. This non-hardening characteristic helps prevent cracking when the alloy is exposed to high temperatures or welded. 410S is completely ferritic in the annealed condition. It exhibits adequate corrosion resistance similar to 410 and good oxidation resistance.
Chemical Composition (%)
Grade | C | Mn | Si | P | S | Cr | Ni |
410S | ≤0.08 | ≤1.00 | ≤1.00 | ≤0.04 | ≤0.03 | 11.5-13.5 | ≤0.6 |
Mechanical Properties
Yield Strength 0.2% Offset |
Ultimate Tensile Strength |
Elongation in 2 in.% |
Hardness Rockwell B |
Reduction percent of area |
||
psi | (MPa) | psi | (MPa) | |||
42,000 | 290 | 64,400 | 444 | 33 | 75 | 65 |
Characteristics
The alloy can not be hardened by heat treatment. It is annealed in the 1600 – 1650°F (871 – 899°C) range and then air cooled to relieve cold working stresses. 410S should not be exposed to temperatures of 2000°F (1093°C) or above due to embrittlement. If excessive large grains are encountered after annealing mildly cold-worked material, the annealing temperature should be decreased to a range of 1200 – 1350°F (649 – 732°C) range.
For maximum corrosion resistance to chemical environments, it is essential that the 410S surface be free of all heat tint or oxide formed during annealing or hot working. All surfaces must be ground or polished to remove any traces of oxide and surface decarburization. The parts should then be immersed in a warm solution of 10-20% nitric acid followed by a water rinse to remove any residual iron.
Alloy 410S should be machined in the annealed condition using surface speeds of 60 to 80 feet (18.3 – 24.4 m) per minute.
For maximum corrosion resistance to chemical environments, it is essential that the 410S surface be free of all heat tint or oxide formed during annealing or hot working. All surfaces must be ground or polished to remove any traces of oxide and surface decarburization. The parts should then be 410S is generally considered to be weldable by the common fusion and resistance techniques. Special consideration should be given to avoid brittle weld fractures during fabrication by minimizing discontinuities, maintaining low weld heat input and occasionally warming the part somewhat before forming. 410S is generally considered to have slightly poorer weldability than the most common ferritic stainless steel grade 409. A major difference can be attributed to the alloy addition to control hardening which results in the need for higher heat input to achieve penetration during arc welding. When a weld filler is required, AWS E/ER 309L or 430 filler material is most often specified. Immersed in a warm solution of 10-20% nitric acid followed by a water rinse to remove any residual iron.
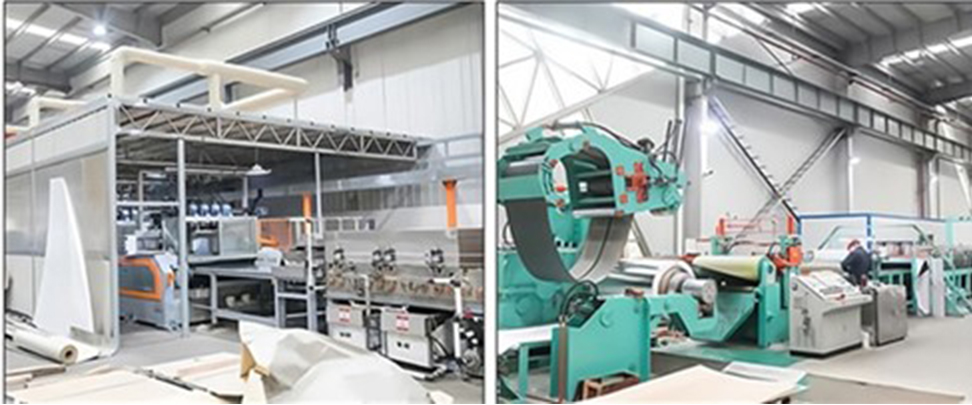