Inox Sheet Metal 4ft X 8ft 304L Stainless Steel Plate Price Per Kg
Product Description
Alloy 304/304L (UNS S30400/S30403) is the most widely utilized “18-8” chromium-nickel austenitic stainless steel. It is an economical and versatile corrosion resistant alloy suitable for a wide range of general purpose applications.
It is common practice for 304L to be dual certified as 304 and 304L. The low carbon chemistry of 304L combined with an addition of nitrogen enables 304L to meet the mechanical properties of 304.
Alloy 304/304L resists atmospheric corrosion, as well as, moderately oxidizing and reducing environments. The alloy has excellent resistance to intergranular corrosion in the as-welded condition. Alloy 304/304L has excellent strength and toughness at cryogenic temperatures.
Alloy 304/304L is non-magnetic in the annealed condition, but can become slightly magnetic as a result of cold working or welding. It can be easily welded and processed by standard shop fabrication practices.
Chemical Composition (%):
Grade | C | Mn | Si | P | S | Cr | Ni |
304L | ≤0.03 | ≤2.0 | ≤1.0 | ≤0.045 | ≤0.03 | 18.0-20.0 | 9.0-12.0 |
Processing Method
Working temperatures of 1652–2102°F (750–1150°C) are recommended for most hot working processes. For maximum corrosion resistance, the material should be annealed at 1900°F (1038°C) minimum and water quenched or rapidly cooled by other means after hot working.
The alloy is quite ductile and forms easily. Cold working operations will increase the strength and hardness of the alloy and might leave it slightly magnetic.
Alloy 304/304L is subject to work hardening during deformation and is subject to chip breaking. The best machining results are achieved with slower speeds, heavier feeds, excellent lubrication, sharp tooling and powerful rigid equipment.
Alloy 304/304L can be easily welded and processed by standard shop fabrication practices.
Operation | Tool | Lubrication | Conditions | |||||
Depth-mm | Depth-in | Feed-mm/t | Feed-in/t | Speed-m/min | Speed-ft/min | |||
Turning | High Speed Steel | Cutting Oil | 6 | .23 | 0.5 | .019 | 13-18 | 42.6-59 |
Turning | High Speed Steel | Cutting Oil | 3 | .11 | 0.4 | .016 | 20-25 | 65.6-82 |
Turning | High Speed Steel | Cutting Oil | 1 | .04 | 0.2 | .008 | 26-31 | 85.3-101.7 |
Turning | Carbide | Dry or Cutting Oil | 6 | .23 | 0.5 | .019 | 75-85 | 246-278.9 |
Turning | Carbide | Dry or Cutting Oil | 3 | .11 | 0.4 | .016 | 90-100 | 295.3-328.1 |
Turning | Carbide | Dry or Cutting Oil | 1 | .04 | 0.2 | .008 | 110-120 | 360.8-393.7 |
Depth of cut-mm | Depth of cut-in | Feed-mm/t | Feed-in/t | Speed-m/min | Speed-ft/min | |||
Cutting | High Speed Steel | Cutting Oil | 1.5 | .06 | 0.03-0.05 | .0012-.0020 | 18-23 | 59-75.5 |
Cutting | High Speed Steel | Cutting Oil | 3 | .11 | 0.04-0.06 | .0016-.0024 | 19-24 | 62.3-78.7 |
Cutting | High Speed Steel | Cutting Oil | 6 | .23 | 0.05-0.07 | .0020-.0027 | 20-25 | 65.6-82 |
Feed-mm/t | Feed-in/t | Speed-m/min | Speed-ft/min | |||||
Milling Profiling | High Speed Steel | Cutting Oil | 0.05-0.10 | .002-.004 | 12-22 | 39.4-72.2 |
Alloy 304/304L is subject to work hardening during deformation and is subject to chip breaking. The best machining results are achieved with slower speeds, heavier feeds, excellent lubrication, sharp tooling and powerful rigid equipment.
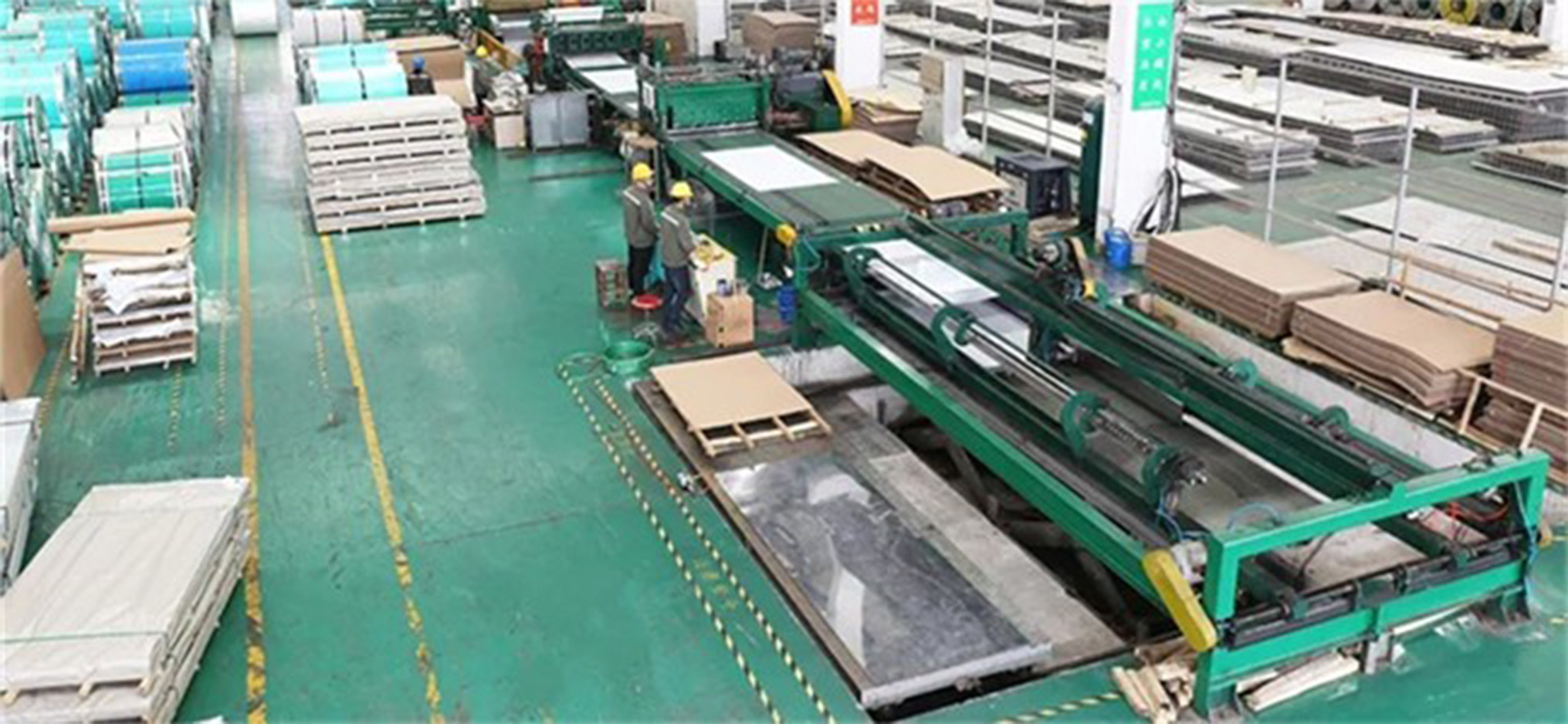
