420J1 Stainless Steel Strips Cold Rolled Stainless Steel Strip
Features
420J1 characteristic of this Martensitic grade is its ability to be hardened by heat treatment. Thus, when quenched they attain high levels of resistance enabling the achievement of a cutting edge. Combined with their good corrosion resistance, this aptitude meets the requirements of many applications. 420J1 stainless steel strip is mostly used to manufacture parts that are resistant to atmospheric, steam, water, and oxidizing acids.
Chemical Composition (%)
Element | Minimum percentage | Maximum percentage |
C | 0.16 | 0.25 |
Si | – | 1.0 |
Mn | – | 1.0 |
P | – | 0.035 |
S | – | 0.03 |
Cr | 12.0 | 14.0 |
Mechanical Properties
Proof Strength Rp0.2 (MPa) |
Tensile Strength Rm (MPa) |
Impact Energy KV (J) |
Elongation at Fracture A (%) | As Heat Treated Condition | Brinell Hardness (HBW) |
136 (≥) | 624 (≥) | 42 | 31 | Solution and Aging, Annealing, Ausaging, Q+T,etc | 314 |
Physical Properties
Thermal expansion | 82-74 | e-6/K |
Thermal conductivity | 23-26 | W/m.K |
Specific heat | 450-460 | J/kg.K |
Melting temperature | 7720-8413 | 째C |
Density | 4702-6397 | kg/m3 |
Resistivity | 0.50-0.60 | Ohm.mm2/m |
Advantages
What is the different between 420J1 stainless steel strip and 420J2 stainless steel strip
420J1 has a certain degree of wear resistance and corrosion resistance, high hardness, and its price is the lower of the stainless steel balls. It is suitable for the working environment that requires ordinary stainless steel.
420J2 stainless steel belt is a brand of stainless steel produced in accordance with American ASTM standards; Japanese standard SUS420J2, new national standard 30Cr13, old national standard 3Cr13, digital code S42030, European standard 1.4028.
420J1 stainless steel: After quenching, the hardness is high, and the corrosion resistance is good (magnetic). After quenching, 420J2 stainless steel is harder than 420J1 steel (magnetic).
Generally, the quenching temperature of 420J1 is 980~1050℃. The hardness of 980℃ heating oil quenching is significantly lower than 1050℃ heating oil quenching. The hardness after 980℃ oil quenching is HRC45-50, and the hardness after 1050℃ oil quenching is 2HRC higher. However, the microstructure obtained after quenching at 1050℃ is coarse and brittle. It is recommended to use 1000℃ heating and quenching to get better structure and hardness.
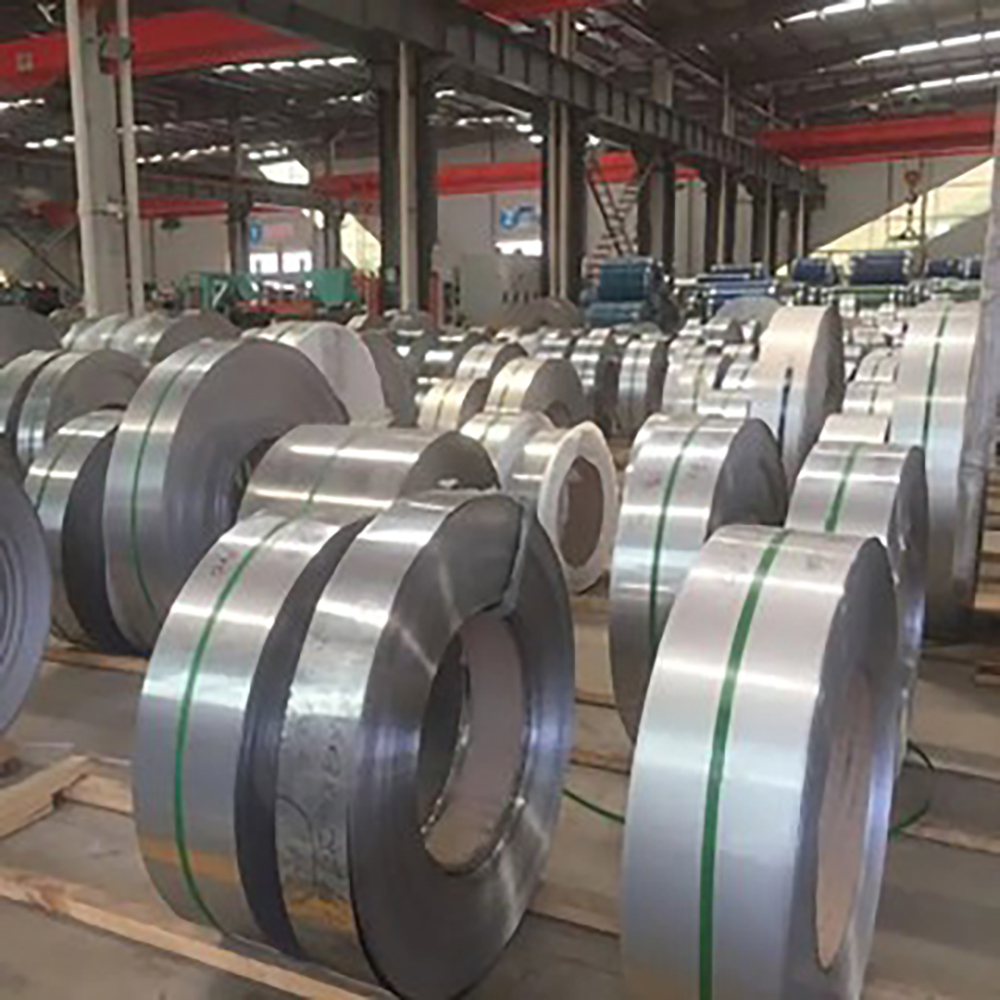
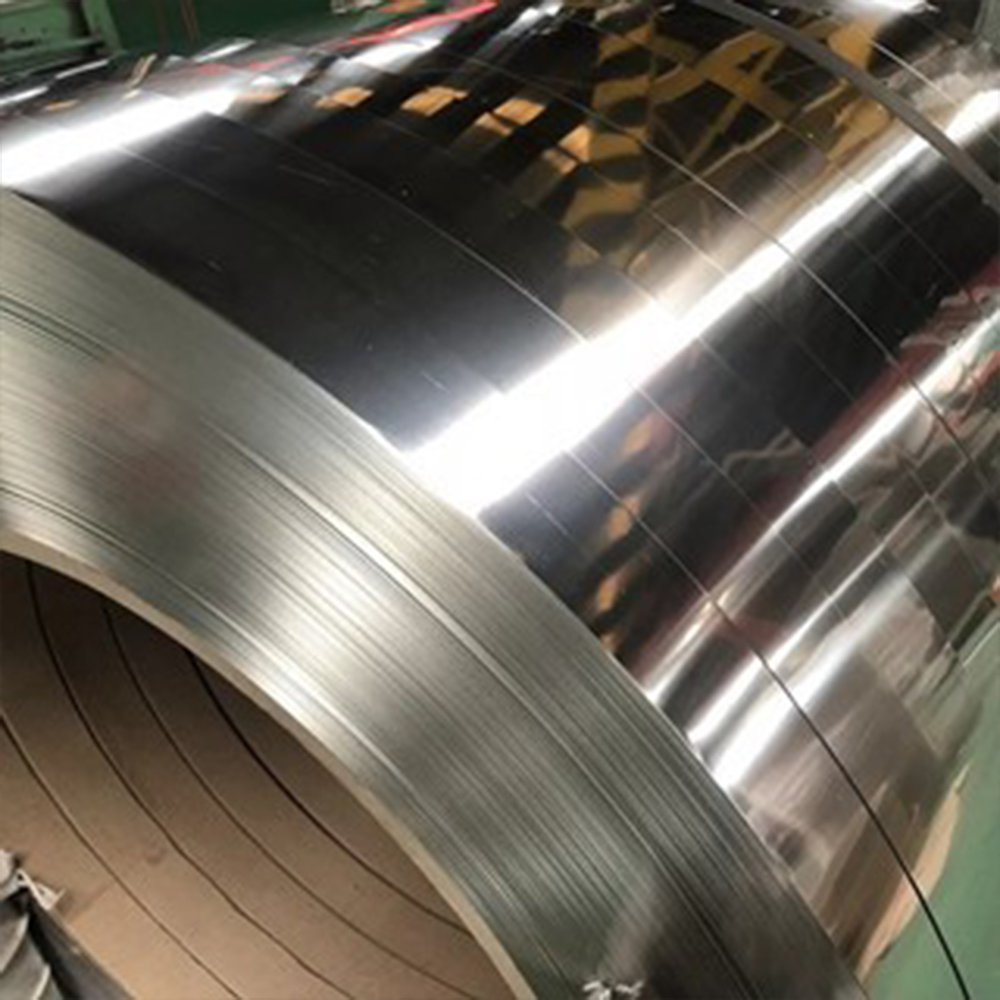