317L Stainless Steel Sheet Coil Cold Rolled Stainless Steel Coil
Characteristics
317L stainless steel coil is one of the most popular stainless steel coils in the market. It is a high strength low-alloy steel, which has good corrosion resistance. The main feature of this metal is its high resistance to corrosion, which makes it ideal for use in chemical plants and marine applications.
In addition, compared with 316L stainless steel coil, 317L stainless steel coil has higher ductility, stress corrosion resistance, compressive strength and high temperature resistance. It is low carbon grade or L grade, this grade has anti-sensitization performance during welding and heat treatment.
Chemical Analysis Weight %
(all values are maximum unless a range is otherwise indicated)
Chromium | 18.0 min.-20.0 max. | Phosphorus | 0.045 |
Nickel | 11.0 min.-15.0 max. | Sulfur | 0.030 |
Molybdenum | 3.0 min. - 4.0 max. | Silicon | 0.75 |
Carbon | 0.030 | Nitrogen | 0.10 |
Manganese | 2.00 | Iron | Balance |
Fabrication Data
Alloy 317L can be easily welded and processed by standard shop fabrication practices.
The alloy is quite ductile and forms easily. The addition of molybdenum and nitrogen implies more powerful processing equipment may be necessary when compared with the standard 304/304L grades.
Working temperatures of 1652 – 2102°F (900 – 1150°C) are recommended for hot working processes. Do not work this alloy below 1742°F (950°C). If the final forming temperature falls below this threshold, a solution anneal of 1976 – 2156°F (1080 – 1180°C) is necessary. Rapid quenching is required.
The cold work hardening rate of Alloy 317L makes it less machinable than 410 stainless steel. The table below provides relevant machining data.
Operation | Tool | Lubrication | Conditions | |||||
Depth
mm |
Depth
in |
Feed
mm/t |
Feed
in/t |
Speed
m/min |
Speed
ft/min |
|||
Turning | High Speed Steel | Cutting Oil | 6 | .23 | 0.5 | .019 | 11-16 | 36-52 |
Turning | High Speed Steel | Cutting Oil | 3 | .11 | 0.4 | .016 | 18-23 | 59-75 |
Turning | High Speed Steel | Cutting Oil | 1 | .04 | 0.2 | .008 | 25-30 | 82-98 |
Turning | Carbide | Dry or Cutting Oil | 6 | .23 | 0.5 | .019 | 70-80 | 230-262 |
Turning | Carbide | Dry or Cutting Oil | 3 | .11 | 0.4 | .016 | 85-95 | 279-313 |
Turning | Carbide | Dry or Cutting Oil | 1 | .04 | 0.2 | .008 | 100-110 | 328-361 |
Depth of cut
mm |
Depth of cut
in |
Feed
mm/t |
Feed
in/t |
Speed
m/min |
Speed
ft/min |
|||
Cutting | High Speed Steel | Cutting Oil | 1.5 | .06 | 0.03-0.05 | .0012-.0020 | 16-21 | 52-69 |
Cutting | High Speed Steel | Cutting Oil | 3 | .11 | 0.04-0.06 | .0016-.0024 | 17-22 | 56-72 |
Cutting | High Speed Steel | Cutting Oil | 6 | .23 | 0.05-0.07 | .0020-.0027 | 18-23 | 59-75 |
Drill ø
mm |
Drill ø
in |
Feed
mm/t |
Feed
in/t |
Speed
m/min |
Speed
ft/min |
|||
Drilling | High Speed Steel | Cutting Oil | 1.5 | .06 | 0.02-0.03 | .0007-.0012 | 10-14 | 33-46 |
Drilling | High Speed Steel | Cutting Oil | 3 | .11 | 0.05-0.06 | .0020-.0024 | 12-16 | 39-52 |
Drilling | High Speed Steel | Cutting Oil | 6 | .23 | 0.08-0.09 | .0031-.0035 | 12-16 | 39-52 |
Drilling | High Speed Steel | Cutting Oil | 12 | .48 | 0.09-0.10 | .0035-.0039 | 12-16 | 39-52 |
Feed
mm/t |
Feed
in/t |
Speed
m/min |
Speed
ft/min |
|||||
Milling Profiling | High Speed Steel | Cutting Oil | 0.05-0.10 | .002-.004 | 10-20 | 33-66 |
Alloy 317L can be readily welded by most standard processes. A post weld heat treatment is not necessary
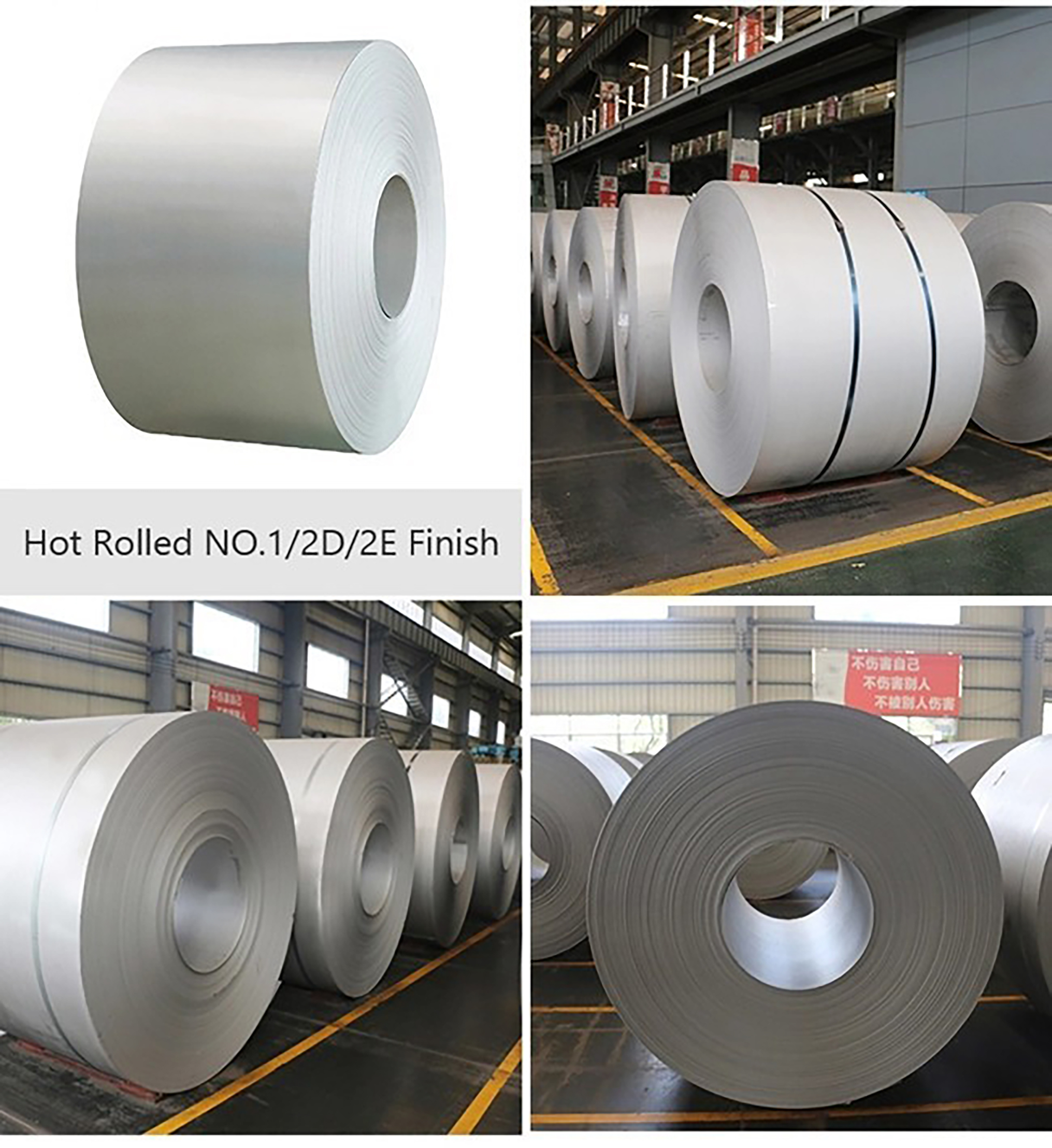