316L Stainless Steel Sheet Coil Stainless Coil 316L 0.5mm 0.6mm
Characteristics
316L stainless steel coil is an austenitic stainless steel that offers both good corrosion resistance and high strength. It has similar mechanical properties to 304L coil but is more resistant to pitting and crevice corrosion.
316L stainless steel has a maximum carbon content of 0.03, which can be used in applications that cannot be annealed after welding and require maximum corrosion resistance. 316L stainless steel coils contain 12 to 15% nickel, with an average of 14%. This code is the American and Japanese models, China's model is 0Cr17Ni14Mo2. 316L (316) is the second most widely used stainless steel after 304 stainless steel. Its main characteristics are acid and alkali resistance and high-temperature resistance. It is mainly used in food industry and surgical equipment. 316L contains 2% more nickel than 316, so it is more resistant to acid and alkali and high temperature.
Chemical Analysis Weight %
(all values are maximum unless a range is otherwise indicated)
Element | 316 | 316L |
Chromium | 16.0 min.-18.0 max. | 16.0 min.-18.0 max. |
Nickel | 10.0 min.-14.0 max. | 10.0 min.-14.0 max. |
Molybdenum | 2.00 min.-3.00 max. | 2.00 min.-3.00 max. |
Carbon | 0.08 | 0.030 |
Manganese | 2.00 | 2.00 |
Phosphorus | 0.045 | 0.045 |
Sulfer | 0.03 | 0.03 |
Silicon | 0.75 | 0.75 |
Nitrogen | 0.1 | 0.1 |
Iron | Balance | Balance |
Fabrication Data
Alloy 316/316L can be easily welded and processed by standard shop fabrication practices.
Working temperatures of 1700 – 2200°F (927 – 1204°C) are recommended for most hot working processes. For maximum corrosion resistance, the material should be annealed at 1900°F (1038°C) minimum and water quenched or rapidly cooled by other means after hot working.
The alloy is quite ductile and forms easily. Cold working operations will increase the strength and hardness of the alloy and might leave it slightly magnetic.
Alloy 316/316L is subject to work hardening during deformation and is subject to chip breaking. The best machining results are achieved with slower speeds, heavier feeds, excellent lubrication, sharp tooling and powerful rigid equipment.
Operation | Tool | Lubrication | Conditions | |||||
Depth-mm | Depth-in | Feed-mm/t | Feed-in/t | Speed-m/min | Speed-ft/min | |||
Turning | High Speed Steel | Cutting Oil | 6 | .23 | 0.5 | .019 | 11-16 | 36.1-52.5 |
Turning | High Speed Steel | Cutting Oil | 3 | .11 | 0.4 | .016 | 18-23 | 59.1-75.5 |
Turning | High Speed Steel | Cutting Oil | 1 | .04 | 0.2 | .008 | 25-30 | 82-98.4 |
Turning | Carbide | Dry or Cutting Oil | 6 | .23 | 0.5 | .019 | 70-80 | 229.7-262.5 |
Turning | Carbide | Dry or Cutting Oil | 3 | .11 | 0.4 | .016 | 85-95 | 278.9-312.7 |
Turning | Carbide | Dry or Cutting Oil | 1 | .04 | 0.2 | .008 | 100-110 | 328.1-360.9 |
Depth of cut-mm | Depth of cut-in | Feed-mm/t | Feed-in/t | Speed-m/min | Speed-ft/min | |||
Cutting | High Speed Steel | Cutting Oil | 1.5 | .06 | 0.03-0.05 | .0012-.0020 | 16-21 | 52.5-68.9 |
Cutting | High Speed Steel | Cutting Oil | 3 | .11 | 0.04-0.06 | .0016-.0024 | 17-22 | 55.8-72.2 |
Cutting | High Speed Steel | Cutting Oil | 6 | .23 | 0.05-0.07 | .0020-.0027 | 18-23 | 59-75.45 |
Drill ø mm | Drill ø in | Feed-mm/t | Feed-in/t | Speed-m/min | Speed-ft/min | |||
Drilling | High Speed Steel | Cutting Oil | 1.5 | .06 | 0.02-0.03 | .0008-.0012 | 10-14 | 32.8-45.9 |
Drilling | High Speed Steel | Cutting Oil | 3 | .11 | 0.05-0.06 | .0020-.0024 | 12-16 | 39.3-52.5 |
Drilling | High Speed Steel | Cutting Oil | 6 | .23 | 0.08-0.09 | .0031-.0035 | 12-16 | 39.3-52.5 |
Drilling | High Speed Steel | Cutting Oil | 12 | .48 | 0.09-0.10 | .0035-.0039 | 12-16 | 39.3-52.5 |
Alloy 316/316L can be readily welded by most standard processes. A post weld heat treatment is not necessary.

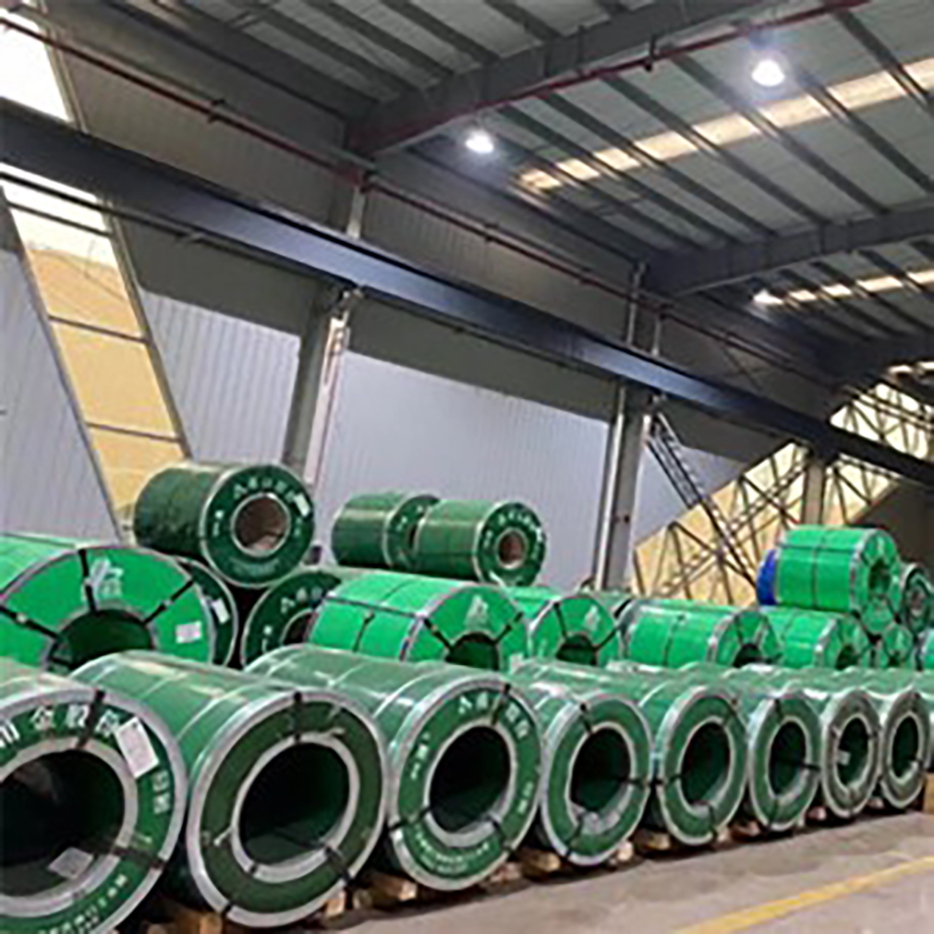
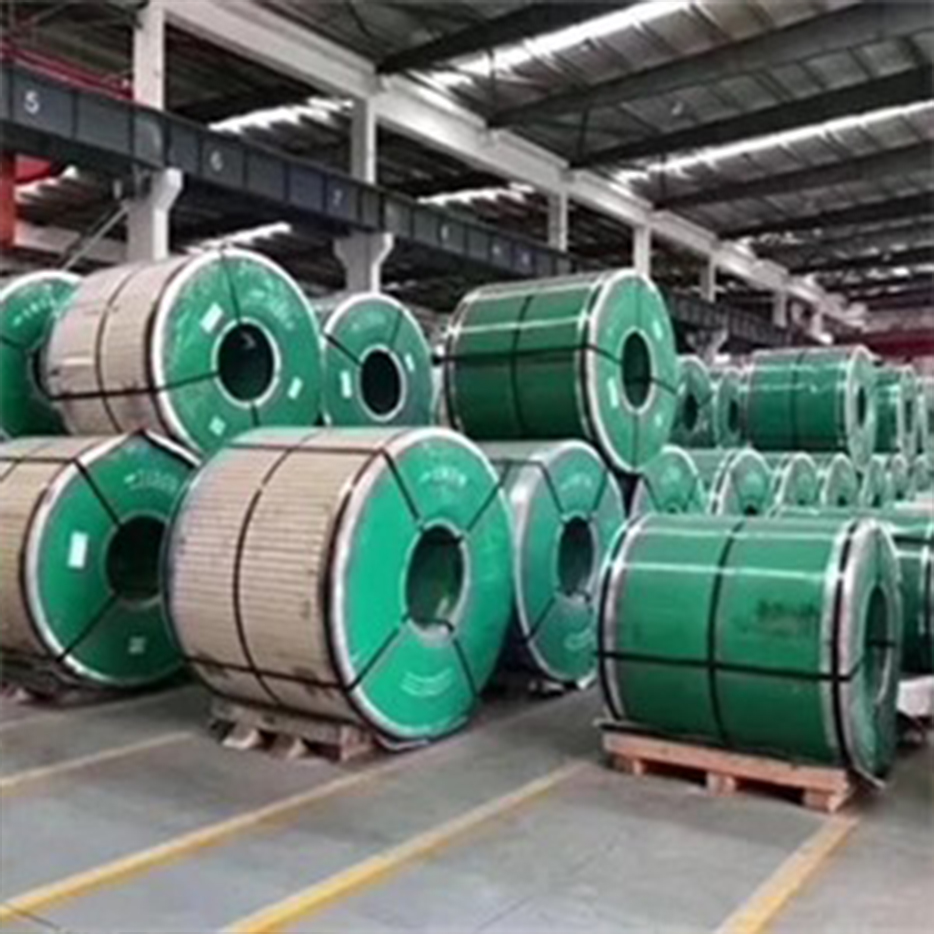